The Ultimate Guide to Industrial Equipment Maintenance: Tips and Best Practices
When it comes to keeping your industrial equipment running smoothly and efficiently, regular maintenance is key. Proper maintenance not only ensures the longevity of your equipment but also minimizes downtime and costly repairs. In this guide, we will provide you with essential tips and best practices for industrial equipment maintenance.
Importance of Regular Maintenance
Regular maintenance is crucial for industrial equipment as it helps prevent unexpected breakdowns and extends the lifespan of your machinery. By following a proactive maintenance schedule, you can identify issues before they escalate into major problems. This saves you both time and money in the long run.
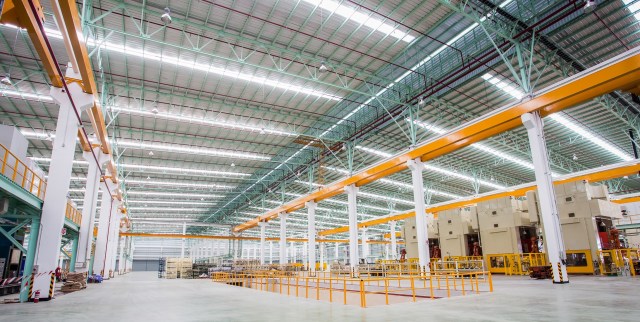
One of the primary benefits of regular maintenance is improved safety. Faulty equipment can pose serious risks to employees, leading to accidents or injuries. By conducting routine inspections and addressing any issues promptly, you create a safer working environment for everyone.
Creating a Maintenance Schedule
To ensure that your industrial equipment receives proper attention, it’s essential to establish a comprehensive maintenance schedule. Start by identifying all the critical components that require regular inspections or servicing. This could include motors, belts, bearings, filters, lubrication systems, electrical connections, and more.
Once you have identified the components that need attention, determine how frequently each item should be inspected or serviced. Some components may require daily checks while others may only need monthly or quarterly attention. Consider manufacturer recommendations as well as your own experience with the equipment when setting up your schedule.
Conducting Routine Inspections
Routine inspections play a vital role in maintaining industrial equipment. These inspections should cover both visual checks and functional tests to ensure that everything is in proper working order.
Visual checks involve examining various parts of the machinery for signs of wear or damage such as loose bolts or leaks. It’s important to pay close attention to warning indicators like abnormal noises or vibrations during these inspections.
Functional tests involve running the machinery to assess its performance. This could include checking for proper alignment, verifying accurate readings on gauges, or testing the equipment under normal operating conditions. Regular functional tests help you identify any potential issues and take corrective action before they cause significant problems.
Regular Cleaning and Lubrication
Cleaning and lubrication are essential maintenance tasks that should not be overlooked. Dust, dirt, or debris can accumulate on machinery, leading to clogged filters or impaired performance. Regularly cleaning your equipment helps prevent these issues.
Lubrication is equally crucial as it reduces friction between moving parts, minimizing wear and tear. Refer to the manufacturer’s recommendations for the appropriate type and frequency of lubrication for each component. Maintaining proper lubrication ensures smooth operation and extends the lifespan of your industrial equipment.
In conclusion, regular maintenance is vital for keeping industrial equipment in optimal condition. By following a proactive approach and implementing a comprehensive maintenance schedule, you can minimize downtime, improve safety, and extend the lifespan of your machinery. Remember to conduct routine inspections, clean your equipment regularly, and ensure proper lubrication to keep everything running smoothly.
This text was generated using a large language model, and select text has been reviewed and moderated for purposes such as readability.